ECS is now your trusted source for Eaton engine and clutch valves.
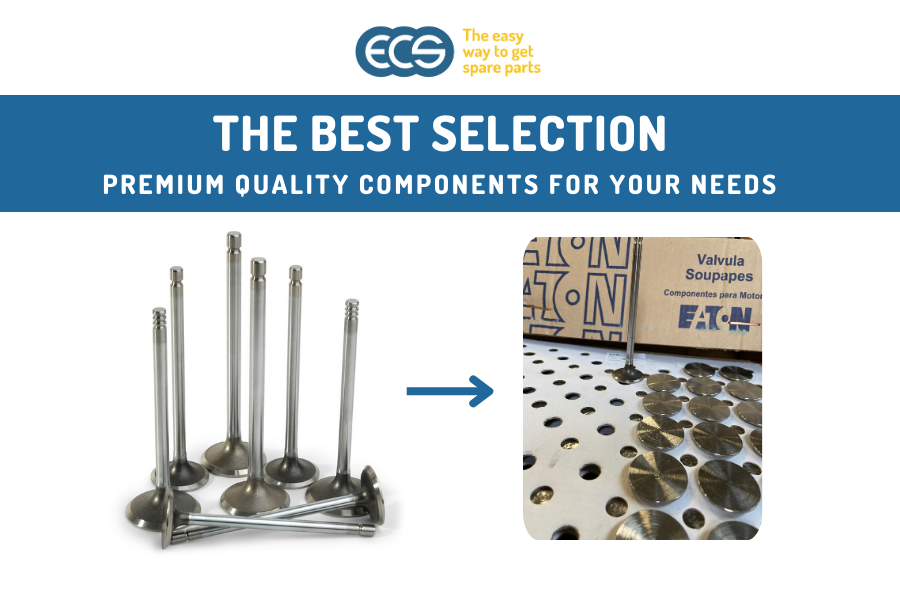
We at ECS are thrilled to kick off the new year with an exciting announcement: we can now supply Eaton engine and clutch valves! This is a significant milestone for our company and strengthens our commitment to providing our customers with top-quality, cutting-edge solutions. We’re proud to offer EATON components—renowned for their excellence and innovation in the energy management industry.
Who is Eaton?
If you’re not yet familiar with Eaton, let us introduce you. Eaton is a global leader in intelligent power management, boasting over a century of innovation and excellence. The company develops state-of-the-art solutions to help industries and businesses worldwide manage power more efficiently, safely, and sustainably.
Their mission? To improve the quality of life and protect the environment, focusing on sustainability and technological progress. Eaton operates across various sectors, including electrical, aerospace, hydraulic, and automotive, offering products that guarantee reliability and high performance. Their values align perfectly with our vision at ECS: providing the best solutions to ensure top performance in every application.
In the field of engine solutions, Eaton provides engine valves and valve actuation systems that enhance the efficiency and performance of internal combustion engines. These components are designed to optimize airflow and fuel control, contributing to more efficient combustion and reduced emissions.
ECS now offers Eaton engine and clutch valves
Valves are critical components in hydraulic systems, as they regulate fluid flow and pressure, ensuring the proper functioning of machinery and vehicles. Eaton offers a wide range of valves designed to meet the needs of various applications, delivering reliable and long-lasting performance.
Eaton is the leading global supplier of engine valves, supplying nearly all vehicle and engine manufacturers worldwide.
Solutions such as hollow valve manufacturing, seat welding, salt bath nitriding, and continuous materials and coatings development overcome the issues of increased temperatures, combustion pressures, corrosion and seat wear.
For more than 85 years, Eaton has been designing and developing engine valve technologies for manufacturers that require high quality valves for gasoline, diesel and alternative fuel engines.
At ECS we can now provide a comprehensive range of engine and clutch valves to meet even the most demanding and specific requirements. Whether you work in industrial, automotive, or aerospace applications, we have the right solution for you.
Types of valves available
Eaton’s advanced valve actuation technologies are engineered to deliver superior valvetrain dynamics, optimizing performance with reduced friction and minimal component degradation. Featuring rocker arms, roller rocker arms, hydraulic lifters, and hydraulic lash adjusters, all the solutions ensure accurate valve lash control while promoting low-friction, maintenance-free operation for the entire lifespan of the engine.
Eaton provides different types of valves to meet specific application requirements:
Servo valves
Eaton’s Vickers servo valves offer precise closed-loop control, ensuring accurate positioning, repeatable speed profiles, and calculated force or torque adjustment. They outperform competitors even in the most demanding applications.
Overcenter and counterbalance valves
These valves eliminate vibrations, enhancing machine stability and safety. They provide quiet operation, improve working conditions for operators, reduce pressure losses, and increase system efficiency.
Self-leveling valves
These inline-mounted flow dividers automatically adjust the position of buckets or attachments in response to arm cylinder movement, ensuring consistent leveling and enhancing operator productivity.
Load-holding valves
Also known as counterbalance valves, they prevent unwanted actuator movement when a machine arm must remain in a specific position for extended periods, ensuring operational safety and efficiency.
We’re excited to bring these cutting-edge solutions to our customers. At ECS, we believe that quality makes all the difference, and we’re ready to take our service to the next level.
Innovative designs and materials for superior performance
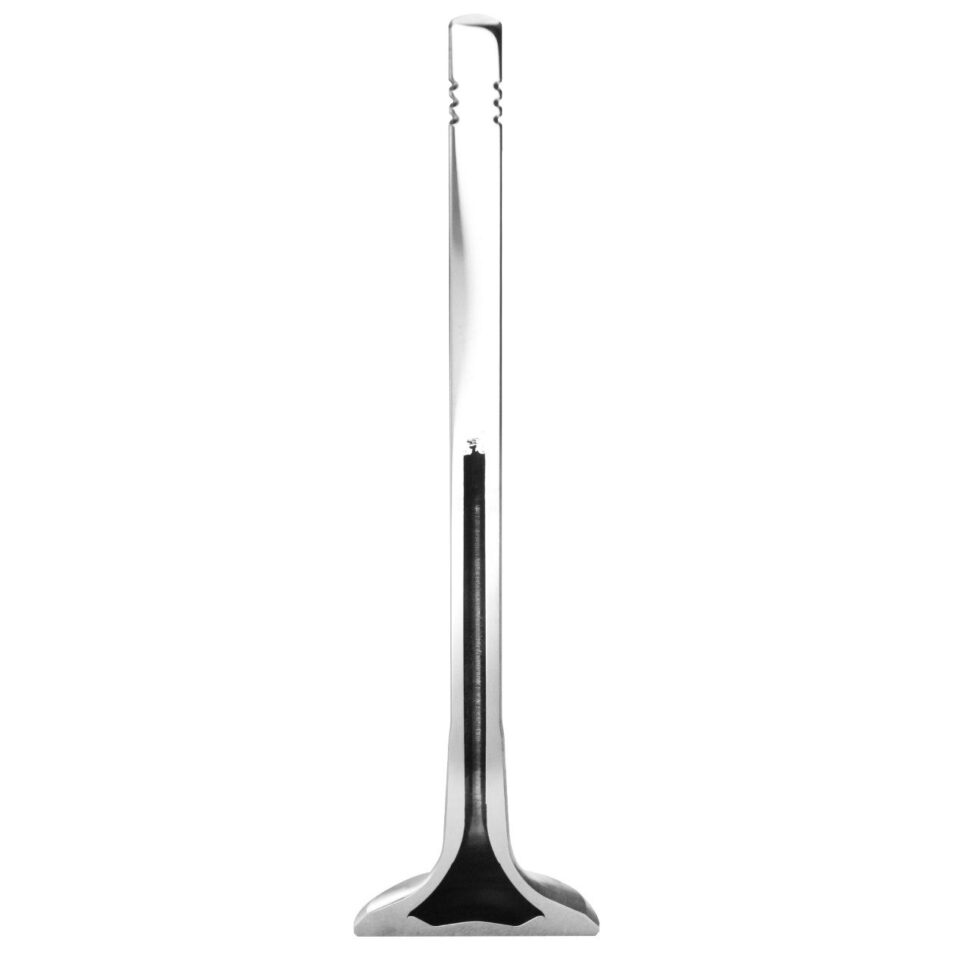
Eaton stands out in the industry by leveraging cutting-edge technology to manufacture high-quality engine valves that meet the evolving demands of modern engines.
With the trend toward engine downsizing and increasing power density, today’s valves must withstand greater mechanical and thermal stresses.
To address these challenges, Eaton utilizes advanced materials, specialized seat and stem coatings, and lightweight hollow valve designs that enhance internal cooling capabilities.
Image taken from Eaton official Website
Superior wear resistance solutions
To ensure durability and optimal performance across various applications, Eaton incorporates a range of high-performance materials and coatings:
- Advanced alloys: Martensitic, Austenitic, and Ni-based alloys provide excellent resistance to high temperatures and oxidation in demanding environments.
- Crutonite™ base material: offers superior seat wear resistance without the need for additional facing.
- High-Temperature seat facing materials: iron, nickel, and cobalt-based alloys are used to enhance wear resistance under extreme conditions, such as dry fuel applications and high-performance settings.
- Stem coatings: designed to improve stem wear resistance for prolonged valve lifespan.
- Thermal barrier coatings: help retain gas energy by minimizing enthalpy loss.
- PVD coatings: enhance gas flow dynamics while reducing carbon buildup, ensuring cleaner and more efficient engine operation.
Proven reliability for high-power applications
Eaton’s innovative valve designs contribute to enhanced engine performance and reliability in high-power, compact engines:
- Lightweight intake valves: designed to reduce mass and improve engine response.
- Sodium-cooled hollow exhaust valves: these valves effectively lower weight while increasing durability, making them ideal for high-performance downsized engines.
- Hollow head valves: further reduce mass and enhance resistance to engine knock, ultimately improving efficiency in terms of fuel consumption and overall performance.
By integrating these advanced technologies, Eaton continues to set new standards in the automotive industry, delivering reliable and efficient solutions that meet the growing demands of modern powertrains.
Crutonite: Eaton’s award-winning High-Temperature Valve Alloy
Crutonite (EMS 200) is Eaton’s proprietary high-temperature exhaust valve alloy that has received the prestigious Automotive News PACE Award for its innovative properties and performance. Designed with reduced nickel content, Crutonite offers a cost-effective solution for both intake and exhaust valve applications, providing an exceptional balance of mechanical strength, wear resistance, and corrosion protection.
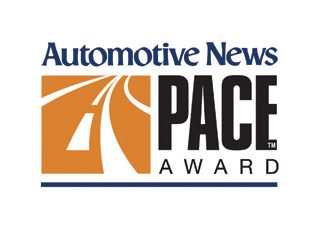
Key Features and Benefits of Crutonite
- Superior mechanical and physical properties:
- Crutonite outperforms conventional iron-based austenitic stainless steel alloys and offers properties comparable to high-end nickel-based superalloys, ensuring durability and longevity under extreme operating conditions.
- Enhanced seat wear resistance:
- Unlike traditional alloys, Crutonite provides superior seat wear resistance without the need for additional seat facing, reducing production complexity and cost.
- Cost-effective corrosion resistance:
- Crutonite delivers the same level of acid corrosion resistance as nickel-based superalloys, making it an ideal choice for EGR (Exhaust Gas Recirculation) diesel engines, all at a lower cost.
- Reduced nickel content:
- Featuring up to 40% less nickel content compared to conventional nickel-based superalloys, Crutonite minimizes exposure to volatile market price fluctuations, offering a more economical and stable solution.
By leveraging Crutonite, manufacturers can achieve improved performance, durability, and cost savings, making it a strategic choice for modern, high-performance engine applications.
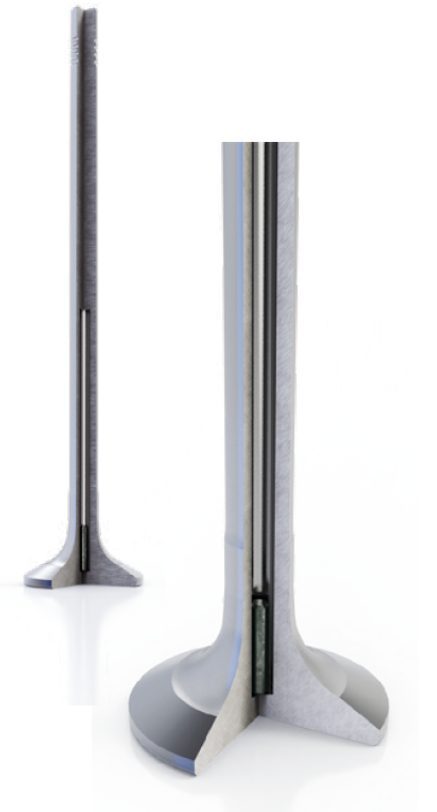
Challenges of Hydrogen Internal Combustion Engines (H2 ICE)
Hydrogen internal combustion engines (H2 ICE) present unique challenges compared to traditional diesel engines.
One of the primary concerns is the elevated combustion chamber temperatures, which increase the likelihood of surface auto-ignition, commonly known as knocking.
Additionally, the high-pressure and high-temperature environment inherent to hydrogen combustion can lead to material embrittlement and accelerated wear, posing significant durability issues.
Eaton’s solutions: advanced materials and innovative valve designs
To overcome these challenges, Eaton has developed proprietary materials and cutting-edge engineering solutions tailored for hydrogen-powered engines:
Crutonite: a specialized solution for H2 ICE challenges
Eaton’s proprietary Crutonite alloy is designed to endure the extreme operating conditions of hydrogen combustion. This material provides excellent resistance to embrittlement and wear, ensuring prolonged durability and reliability in hydrogen engine applications.
Next-generation hollow valve technology
Eaton has also introduced an advanced hollow valve design, specifically developed for hydrogen-powered commercial vehicles. This innovative design effectively lowers operating temperatures across the valve, minimizing the risk of knocking and allowing the use of more cost-efficient materials, making it an optimal solution for H2 ICE engines.
Through the combination of Crutonite’s enhanced durability and the next-generation hollow valve design, Eaton provides robust solutions to meet the demands of hydrogen internal combustion engines, ensuring improved performance, longevity, and cost-effectiveness.
Want to learn more about Eaton valves?
Contact us to discover how we can help you find the perfect solution for your needs.