Cheap spare parts will cost you more in the long run
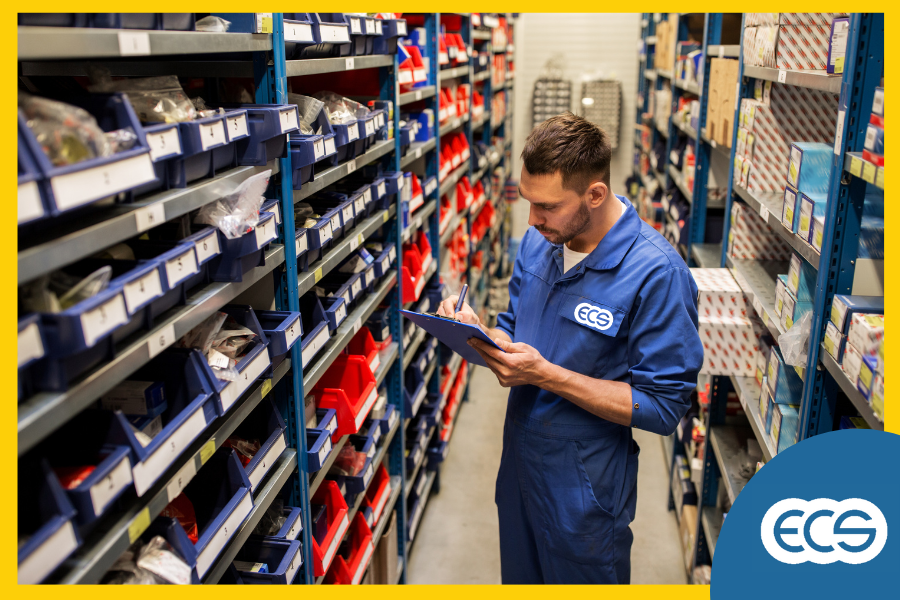
At ECS we aim to offer a high quality service to our customers. We are convinced that paying the utmost attention and ensuring total commitment in providing our services is an important distinctive and identifying element of our company.
We work with excellent brands and suppliers, but our mission goes beyond simply sending spare parts to customers who request them, we want to offer a top service and take care of our customers and make them fully satisfied for having chosen to turn to us.
We have often found ourselves facing the stinging situation of a competition that offers the same spare parts at lower prices than ours. We could choose to further lower prices and compete economically. But this attitude is totally at odds with the level of quality and care we want to guarantee our customers.
Why using cheap replacement parts can end up costing you more?
We do not judge those who make an exclusively economic choice by turning to the supplier that offers the part at the lowest price, but we would like to draw attention to the fact that cheap spare parts can often cost more in the long run.
This is because spare parts are often sent to those who ordered them without any additional control, with the risk that the part itself may present anomalies, defects, or malfunctions and must therefore be returned and replaced. This leads to extended waiting times, which often results in economic damage. Additionally, the installation of defective parts can compromise the operation and reliability of the entire system, leading to potential malfunctions and secondary damage that require costly interventions.
Using cheap spare parts in a truck can have several negative consequences. Lower quality materials can reduce the durability of the parts, increasing the frequency of replacements. Inferior quality also increases the risk of mechanical failures, which can lead to unexpected and costly repairs.
Additionally, cheap components can compromise safety, putting the driver and other road users at risk.
Although they offer initial savings, long-term costs can be higher due to frequent replacements and additional repairs.
They can also affect the operational efficiency of the truck, increasing fuel consumption and reducing productivity.
Using non-original parts can invalidate the manufacturer’s warranties and negatively affect the company’s reputation, resulting in the loss of customers and contracts. In some cases, these spare parts may not comply with local or international regulations, which can lead to fines and penalties.
The pursuit of immediate savings can result in much higher expenses over time. It is important to carefully evaluate the cost-benefit of using high-quality spare parts to maintain the reliability, safety, and operational efficiency of trucks.
Accurate checks
Precisely with the aim of guaranteeing our customers the highest level of quality, from October 2023 we have modified our processes, introducing a specific quality control activity.
We carry out packaging compliance and piece compliance checks on all pieces. Thanks to the use of a special control bench and hoist/crane created specifically to lift and rotate the motors, we carefully examine the condition of the piece to verify that it meets the highest standards.
Specifically, we carry out the following quality controls:
- Visual inspection: check for any visible damage, cracks, casting defects, surface imperfections or deformations.
- Dimensional measurements: verify critical dimensions (such as cam diameter and cam clearance in the case of a camshaft) using micrometers and calipers to ensure they meet specified tolerances. Check critical dimensions, such as bearing bores and crankcase seating surfaces.
- Hardness check: using a durometer to measure the hardness of the material and ensure it meets the required specifications.
- Alignment check: check that the bearing surfaces are aligned correctly.
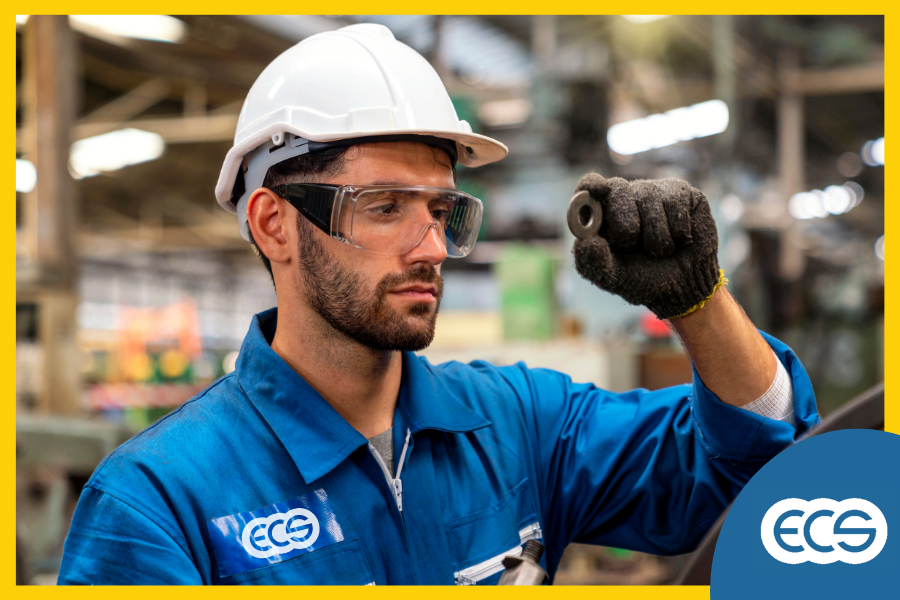
How does our quality check work?
With years of expertise in quality control, our dedicated team meticulously oversees every step of our quality verification process, ensuring the highest standards are consistently met. Here’s how we guarantee excellence in every piece:
- Comprehensive inspections: we conduct full quality checks on all orders from our suppliers to ensure consistent quality.
- 4C Parts Assurance: we perform thorough inspections on critical components including crankshaft, camshaft, crankcase, and cylinder head.
- Engine scrutiny: all our engines are subject to exhaustive quality checks to ensure peak performance.
In case we identify inadequate packaging or potential damage risks, we proactively enhance the piece’s protection with solutions such as barrier bags, desiccants, and specialized lubricants to maintain integrity.
In cases of detected anomalies or imperfections, we take decisive action—from additional inspections to the outright rejection and replacement of the piece, ensuring only the best reach our customers.
At ECS we care about your trust
At ECS we work hard and are committed to gaining and maintaining the trust and maximum credibility of our customers over time. We are not simply interested in selling as much as possible, we want to make sure that our customers are satisfied.
Our reality is made up of people. These are specialized, highly motivated people who love their work and know how to do it well. But we are always people and it can happen that, despite the utmost attention, we too make some mistakes.
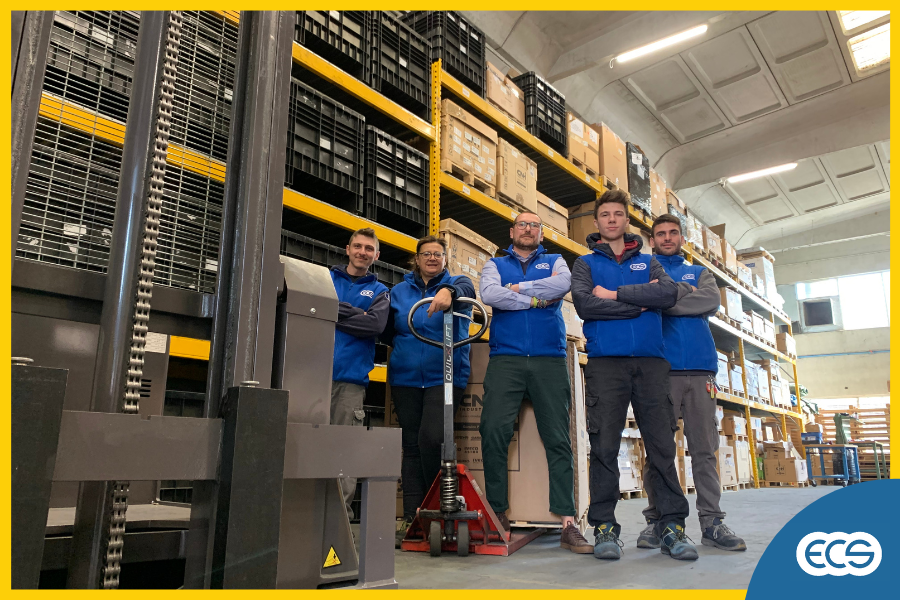
If any issues arise, we are available to quickly and efficiently find a solution together. Your feedback is vital for us to address any concerns promptly and ensure your satisfaction. Please don’t hesitate to contact us at claim@ecsexport.com.